Post mold cure (PMC) is one of the most significant processes in electrical industry. This process exposes part of a mold to elevated temperatures in order to speed up the curing process and to optimize some physical properties of the material.
The post mold cure oven process will expedite the cross-linking process and properly align the polymer’s molecules to make a stronger part with better high temperature characteristics. Much like tempering steel, post curing thermosetting can improve physical properties above what the material would normally achieve at room temperature, such as tensile strength, flexural strength, and can modify the temperature of heat distortion. Moreover, post mold cure process is the most common strategy used today for warpage problem solution. Finally, it can also deal with the outgassing phenomenon during IC package.
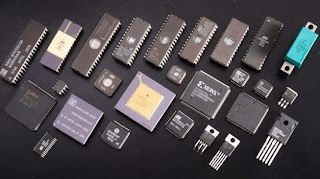
Given the benefits of PMC processing, it is widely used in the electrical device industry. It is easy to find the application of PMC in many facilities and there are a large number of companies using PMC on their products. Figure 1 shows various chips that have been packaged using PMC processes.
PMC Process in IC Encapsulation
There are two major manufacturing steps in IC encapsulation industry. For the first step, the IC chip would be encapsulated into a thermosetting epoxy mold compound (EMC), which is the most common plastic material for IC package manufacture today. This pelletized compound is injected into a hot mold die to form the body around the IC die. And after the plastic injection, the mold is cured. The object of this step is to achieve good fill and partial cure of the mold.
The second step of the process is the post mold cure (PMC) process. The goal of this step is to increase degree of cure and reduce warpage in an IC chip. In order to optimize properties, the PMC process provides a critical completion of the cure process to complete the chemical cross-linking of the material. During PMC, the material experiences additional molecular rearrangement and greater efficiency of molecular collisions resulting in a greater degree of cross linking. The heating can also cause any residual peroxide to break apart and initiate some additional chains.
Generally, a PMC heating process can be divided into three heating stages, assuming that heating process in the furnace is uniform. In the first stage, products are heated from room temperature 25 oC to post mold cure temperature 175 oC in a short time. In the second stage, the temperature is held constant for several hours. In the final stage, the product is cooled from 175 oC to room temperature in a short interval.
Applications of PMC
Post mold cure has been applied by many electronics companies, especially semiconductor designers and manufacturers. Table 1 shows various products that have benefited from PMC to achieve better performance as well as some companies associated with them. From the table, it is easy to see PMC technique is widely used in electronic market by a wide range of corporations. If your company requires better device performance, PMC processing is an easy choice.
A PMC process involves placing the molded articles in a forced-air furnace and thermally treating them to a series of increasing temperatures for various times. The program of times and temperatures is referred to as the cure schedule or cure cycle. During the PMC process, the molecular weight of the polymer increases by chain extension. And as the molecular weight increases virtually all mechanical, chemical, and thermal properties are changed. Figure 2 illustrates how physical properties change during a PMC process. After PMC, the physical properties of objects are substantially increased.
PMC can prevent problems such as warpage during encapsulation in chip packages. In IC encapsulation, one of a prevalent and troublesome EMC defect is warpage. Fortunately, PMC is an efficient method to alleviate the warpage problem during encapsulation. PMC is also one of the principal tools to mitigate outgassing. PMC can remove the volatiles from the cross-linked plastic material. If the volatiles are not removed and the EMC is exposed to elevated temperatures with poor ventilation, one will observe deteriorations in strength, elongation, compression set properties accompanied by chemical decomposition. Insufficient or poor PMC can result in “smoke”, bubbling, delamination and unsightly sticky surface deposits.
To achieve a satisfactory PMC process, the furnace must be tuned to optimize the cure process, which can only be achieved through high quality temperature control. Try reading more
Leave a comment